Polyvinyl Chloride (PVC) is a versatile polymer widely used in various industries, including pipe manufacturing and molding. The modification of PVC involves creating compounds or granules from PVC resin, which enhances its properties for specific applications. This blog will explore the main parameters and processing techniques involved in PVC modification, focusing on its applications in the PVC pipe and molding industries.
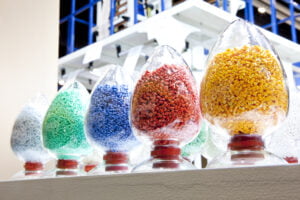
Key Parameters in PVC Modification
-
PVC Resin Properties:
- K Value: This indicates the molecular weight and is crucial for determining the resin's suitability for different applications. A higher K value often means better absorption capacity and flexibility[2].
- Inherent Viscosity: Reflects the fluidity of the molten PVC, impacting the ease of processing[2].
- Particle Size: Affects the dispersion of additives and the overall processing efficiency[2].
-
Additives:
- Plasticizers: Enhance flexibility and impact resistance, essential for applications requiring softer PVC compounds[3].
- Stabilizers: Improve heat stability and weather resistance, crucial for outdoor applications like pipes[3].
- Fillers: Used to modify physical properties and reduce costs, often employed in construction applications[3].
- Lubricants and Pigments: Aid in processing and provide desired aesthetic qualities[5].
-
Impurities and Stabilizers: Impurities can cause processing issues, while stabilizers prevent yellowing and degradation, ensuring the longevity of the final product[2].
Processing Techniques
-
Compounding:
- PVC resin is blended with additives to form a compound tailored for specific applications. This process involves precise formulation to balance performance, processability, and cost-effectiveness[5].
- Differentiation between soft and rigid PVC compounds is achieved by varying the type and amount of plasticizers used. Soft compounds are processed at lower temperatures and exhibit rubber-like properties[5].
-
Extrusion and Molding:
- Extrusion: Used for producing PVC pipes and profiles. The compounded PVC is melted and shaped into continuous profiles through a die. The process parameters are adjusted based on the compound's formulation to ensure optimal flow and cooling[3].
- Injection Molding: Commonly used for creating complex shapes and components. The PVC compound is injected into a mold under high pressure, allowing for detailed and precise products[3].
-
Quality Control:
- Ensures consistency in particle size, additive dispersion, and mechanical properties. Quality control measures are critical to maintaining the high standards required for industrial applications[2].
Applications in PVC Pipe and Molding Industries
- PVC Pipes: Rigid PVC compounds are used due to their durability and chemical resistance. These pipes are widely used in plumbing, sewage, irrigation systems, and electrical conduits. Their ability to withstand high pressure and corrosive environments makes them ideal for these applications[3].
- PVC Molding: Flexible PVC compounds are preferred for molding applications, offering versatility in creating products like seals, gaskets, and various consumer goods. These applications benefit from the material's flexibility, impact resistance, and ability to be molded into complex shapes[3].
Additionally, PVC compounds are used in:
- Medical Devices: Due to their biocompatibility, flexibility, and ease of sterilization, PVC compounds are commonly used in medical tubing, blood bags, and other medical devices.
- Automotive Industry: PVC is used in automotive interiors, wiring harnesses, and under-the-hood applications because of its durability, resistance to chemicals, and ability to withstand high temperatures.
- Construction Materials: PVC compounds are used in the production of flooring, roofing membranes, window frames, and siding, owing to their weather resistance, durability, and low maintenance requirements.
Conclusion
PVC modification through compounding and processing techniques enables the creation of materials with tailored properties for diverse applications. The ability to customize PVC compounds makes them a preferred choice in industries ranging from construction to healthcare. As market demands and technological advancements continue to evolve, ongoing research and development efforts will further enhance the versatility and cost-effectiveness of PVC products.
Citations:
[1] https://www.alibaba.com/showroom/modified-pvc-compound-granules.html
[2] https://chemicalcompounds.com.mx/en/resina-de-pvc-vs-pellets-de-pvc/
[3] https://petronthermoplast.com/difference-between-pvc-resin-and-pvc-compound/
[4] https://pvc-compound.en.made-in-china.com/product/kGtRFoqZXflz/China-High-Quality-Specialty-Plastics-Thermoplastic-Resin-Granules-PVC-Compound.html
[5] https://contacall.com/tr/blog/pvc-compound-production-process-46